TPE TPU Injection Moulding




Polyurethane is the primary material used in polyurethane injection moulding.
We can injection mould in this material!
Lexan is a brand name of Polycarbonate of which we injection mould.
- Flexible
- Rubbery feel
- Wide range of uses
- Hard wearing
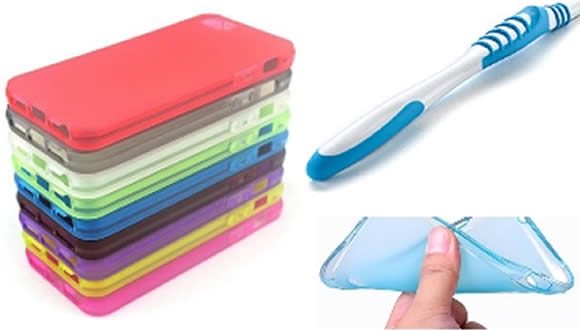
Design and Applications
Polyurethanes are produced in four different forms: elastomers, flexible foams, cross-linked foams and coatings. Out of the four, flexible foams comprise the largest market for polyurethanes and are often found in furniture and mattresses as cushioning material.
Here’s a brief breakdown of polyurethane applications:
Elastomers are used for their strength, flexibility and shock absorption. Used as base materials for footwear, automobile parts and other mechanical goods. TPE injection moulding and TPU injection moulding is a popular material of choice.
Polyurethane coatings are used for their solvent degradation resistance and impact resistance. They’re commonly used on dance floors and in bowling alleys. Water-based versions are used for painting automobiles, aircraft and other industrial equipment.
Cross-linked polyurethanes are used to produce insulation in the form of laminate insulation or board insulation. Laminates are used extensively in commercial roofing and other parts of the construction industry.
Flexible polyurethane foams, as mentioned, are mainly used as cushioning for furniture and mattresses. They’re also used as padding or cushioning for other applications, made into sponges or other cleaning supplies and some forms of packaging.
Background information about Polyurethane as a material.
As mentioned, polyurethane (polycarbamates) belong to a class of compounds known as polymers. Polymers are macromolecules; they’re made from smaller and repeating units known as monomers. They often consist of a main long-chain backbone molecule with smaller attached side groups.
A synthetic polymer, such as polyurethane, is created by reacting monomers in reaction vessels. The step (condensation reaction) that produces polyurethane starts by invoking a chemical reaction between diisoyanate and a diol that produces a reactive alcohol and a reactive isocyanate, which continues to further react with other monomers to produce a larger and long molecule.
Polyurethane’s chemistry was first researched by German chemist Friedrich Bayer in the late 1930s. He produced early prototypes of the material, mainly through reacting toluene diisocyanate with dihydric alcohols.
From this research, the one of the first crystalline polyurethane fibers (Perlon U) was developed. By the mid-1950s, the first commercial production of flexible polyurethane foam had started; by the end of the decade, other forms of pliable polyurethane were well into development and production.
Composition
Various raw materials are used to produce polyurethane. These materials include pre-polymers, monomers, colorants and stabilizers that protect the polymer’s integrity.
Some additives are also included in polyurethane, since there are type of polyurethane that are sensitive to light, heat, chlorine and some atmospheric contaminants. That’s the main reason why stabilizers, such as hydroxybenzotriazole, are added to protect certain grades of polyurethane. That particular stabilizer helps protect some polyurethanes from light degradation.
Some additives are also included in polyurethane.
Since there are type of polyurethane that are sensitive to light, heat, chlorine and some atmospheric contaminants. That’s the main reason why stabilizers, such as hydroxybenzotriazole, are added to protect certain grades of polyurethane. That particular stabilizer helps protect some polyurethanes from light degradation.